Hot Runners Play a Key Role in Optimizing System Balance
Balance has an important influence on the optimization of an injection molding process and can sometimes be a limiting factor in validation. It plays a major role for processors who seek to produce flash-free, fully packed parts with uniform dimensions using the largest possible processing window. Balance is a numeric translation of variation inherent to a specific mold, typically measured by comparing the difference between the heaviest and lightest parts. One of the goals of balance measurement is to minimize that variation, over which hot runners can have a significant influence.
This article will examine the process fundamentals of system and hot runner balance, and its impact on mold qualification. We will look at the factors that facilitate the development of well-designed hot runners, plus the causes of system imbalance. We will also examine the factors that influence short shot balance beyond geometric melt channel balance as well as how to measure system balance and how to set expectations based on specific end-use applications.
Why Worry About Balance?
Cavity balance in injection molding is one of several benchmarks required by the mold qualification process. During the assessment of the molding process, the hot runner can assist in fine-tuning balancing. While there are many sources, such as websites and publications, dedicated to why balance is important, there is little or no information on what constitutes “acceptable” balance. Nor is there widely accepted information on the most effective procedure to measure balance.
For many industry observers, it is unclear what system balance confirms. Does it highlight variation from cavity to cavity, or how much volume is needed to fill the mold? There is a lack of clarity surrounding the definition of injection molding balance, because these determinations are interpreted by the user and subjective in nature.
To have the largest potential process window when injection molding with multicavity tools, all mold cavities should fill at the same time. Cavity-to-cavity and shot-to-shot variation makes it difficult to consistently mold parts with uniform dimensions.
Molded part inconsistencies can take form in a variety of defects. Part inconsistency is obviously not desirable, but what are some of the real consequences of variation? Inconsistency means increased qualification time if a required specification cannot be met. It can increase the cost of poor quality, which can appear as increased scrap rate, additional inspection or increased warranty spend. Part-to-part variation can also limit the process window to make acceptable parts, ultimately reducing flexibility and the robustness of the process.
These results are all “above the water line” and can be measured directly. There are also multiple “below the water line” costs of inconsistent parts. These can be higher risk, expediting, buffer inventory, lost sales, unpredictable profit and loss, diminished customer loyalty and higher administrative costs. By minimizing variation, processors can create a more capable molding system and a mold that can produce more and better parts within the given specification.
Addressing Hot Runner System Imbalance
Short shot balance is affected by many peripherals:
- Injection molding machine (tonnage, platen condition, screw design)
- Resin (type, quality, preparation)
- Processing (injection profile, cooling time, shot size)
- Mold (type of mold, venting, cooling layout, stiffness, part geometry)
Hot runner systems also have several factors that influence short shot balance. Key hot runner considerations include melt channel layout, heater layout, plate bolting and plate cooling. Other influences include gating styles, actuation and temperature control.
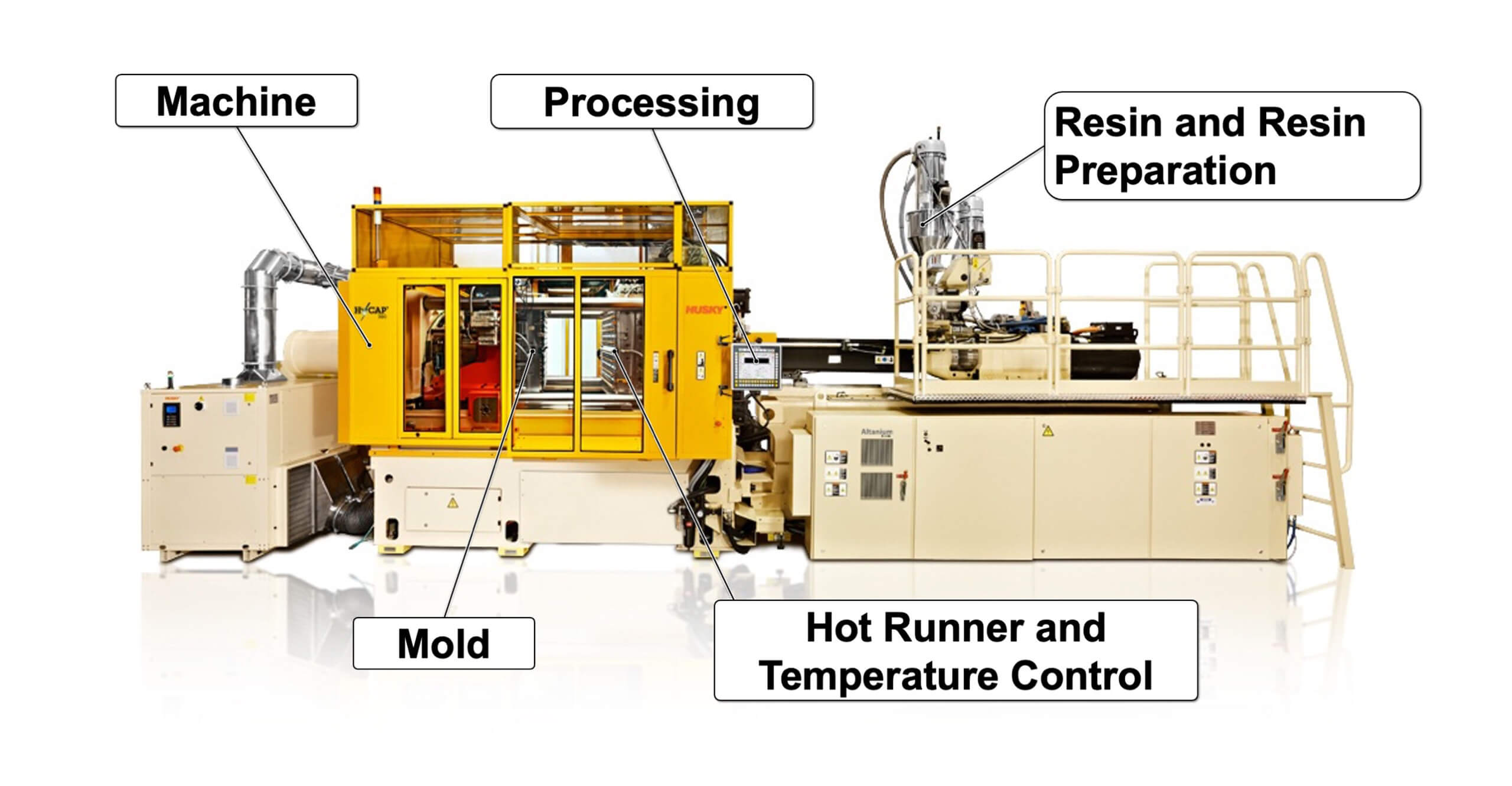
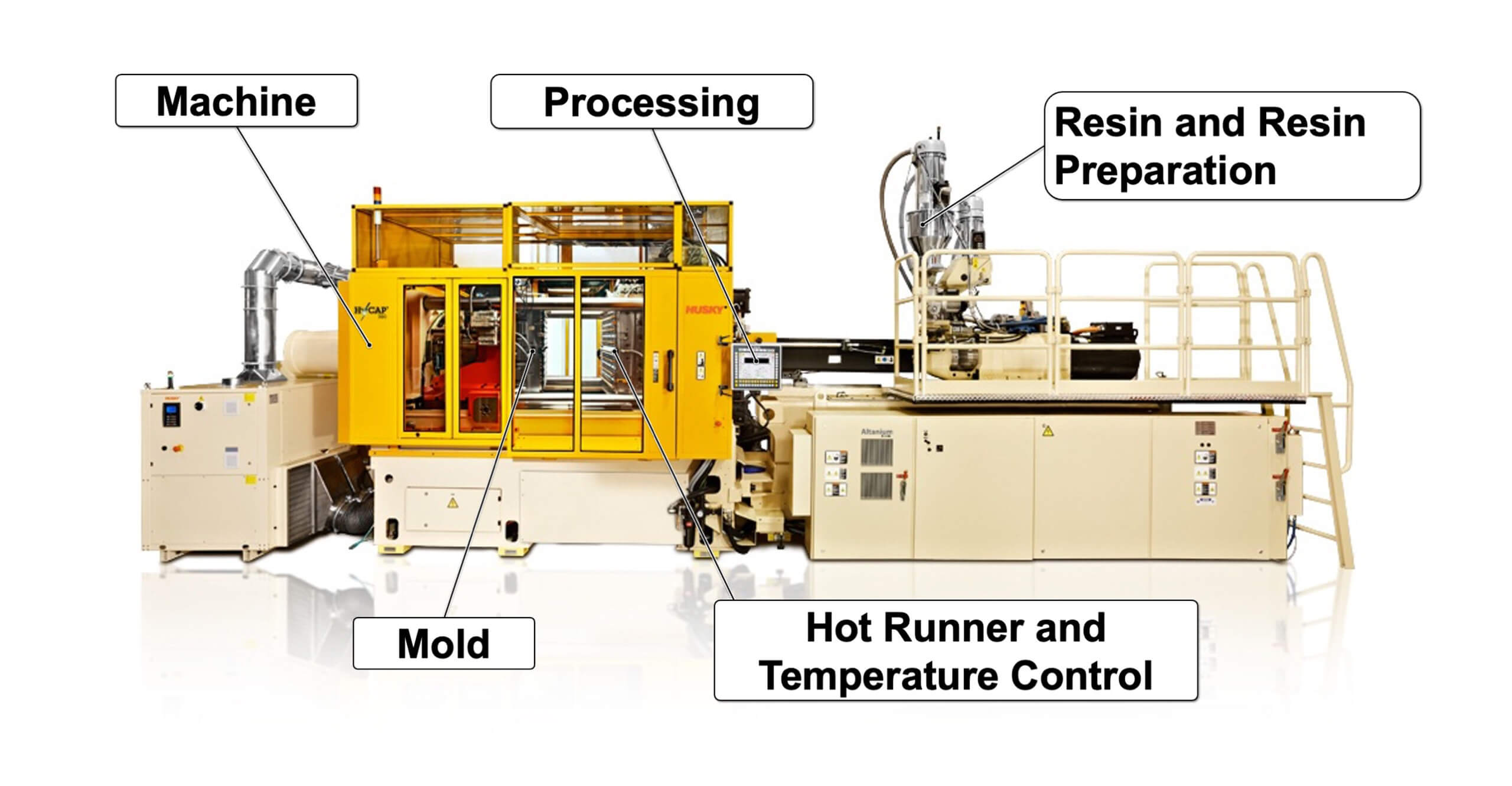
By simply changing resins from PC/ABS to polypropylene, balance on a multicavity tool improved from 65% to 93%. No changes were made to the mold cavity or hot runner to get this improvement, illustrating that resin type can have a large impact on short shot balance. Some resins will have substantial changes in viscosity, with small changes in temperature or shear. The interaction of the resin with processing and tool conditions will be different depending on the properties of the resin. The impact on balance can be positive or negative depending on the resin and tool.
Though hot runners can provide significant benefits to the molder, they increase the complexity of the mold and can also contribute to fill imbalance. When more than one mold cavity is required for molding, the question of balance can become an issue. It is important that all the gates perform identically. This is especially true when molding high-tolerance or thin-wall components for demanding end-use markets, such as medical and healthcare. If the gates do not all behave in the same manner, the mold can become unbalanced. Short shot balancing focuses on the volume of plastic that is less than needed for a fully packed and dimensionally stable part.
Valve stem timing can also have a significant impact on short shot balance. In a 32-cavity syringe barrel mold, short shot balance improved from 60% to 90% by changing valve stem actuation from individual pneumatic pistons for each drop to synchronizing all valve stems with UltraSync® plate actuation.
Thermal Uniformity Creates More Balanced Filling
The goal of a hot runner is to deliver melt to every cavity of a mold, and its thermal profile can also influence balance through optimized design. Ideally, there are identical heat conditions for the resin, regardless of the flow path. Several factors can influence temperature variation, including heater technology, drop layout, manufacturing practices and other design factors. There is an engineered balance between the manifold material, thermocouple placement, heat inputs that occur at heaters and heat losses that occur at the lead-bearing components.
Husky hot runners offer very high levels of thermal uniformity. Their features include:
- Optimized thermal design: Manifolds are designed using strict guidelines based on engineering principles. Thermal finite element analysis (FEA) is used to analyze every manifold design. Heat inputs, heat losses and thermal profile are optimized for each application.
- Validated manufacturing equipment and in-process inspections: Manifold heater manufacture and installation equipment is automated, and process checks are implemented to verify accurate heater element position.
- Thermal uniformity inspection: All finished hot runners and manifold systems are measured and heat tested at final assembly. Prior to shipment, the thermal profile is reviewed against guidelines for compliance, with thermal imaging used to audit and troubleshoot.
Thermal Uniformity Requires Control
A thermally uniform hardware system is only as good as its controller, which relies on accurate temperature signals, optimized and controlled algorithms, and rapid reaction time. The first and most important consideration is the accuracy of the thermocouple signal being used to determine the temperature of the mold. A control algorithm is as effective as the accuracy of the data its calculations are based on. If the temperature measurement is disrupted by high-voltage leaking onto the thermocouple lines, then this will be interpreted as being the correct temperature, when in reality, it is not. The Husky Altanium® mold controller utilizes isolated thermocouple inputs that eliminate the effects of electrical noise and ensure that the temperature signal is true.
The second control component is the control algorithm. The algorithm contains the instructions for modulating the power output to adjust to variations in the process based on feedback from the thermocouples. In the case of the Altanium controller, this process is managed using Active Reasoning Technology (ART), which automatically optimizes the control of each heater to its specific operating environment.
The final control component is reaction time. This is important, because the longer it takes a command to be processed, the more out of tolerance the temperature will be once the calculation from the algorithm is executed. Using a distributed control architecture reduces the distance a signal must travel, which enables commands to be carried out in the shortest amount of time possible.


In a distributed architecture, the temperature control and power-switching circuitry are integrated into a single card. The temperature control algorithm is executed right on the board, allowing the fastest possible reaction time. The operator interface’s primary purpose is to send and monitor configuration parameters to the cards. The result is the most accurate and repeatable temperature control possible.
Gating Options Play a Major Role
The gate is a restricting feature where plastic enters the cavity. Today, hot tip (thermal) gating and valve (mechanical) gating are the two options available for hot runner gating. Static plastic freezes at the gate during hold and creates a membrane or skin that breaks away from the part when the mold opens. The frozen slug left in the gate is blown out at the start of the next cycle. This sequence of this “plug blow” event between several gates can be somewhat random, which can show as imbalance, especially with very high cavitation molds. This is influenced by the slight variation between cavities and gates due to tolerance. Even the supplied resin itself is not truly homogenous, carrying a range of molecular weight. Hot runner temperature setpoints can be adjusted to decrease these influences on balance.
The other gating option—valve gating—is a mechanical method of control, offering higher gate quality. It offers more shot-to-shot consistency compared with thermal gating, because the mechanical opening and closing of the gate eliminates inconsistencies related to thermal gating. Along with no gate vestige issues, the gate diameter is larger, resulting in less gate shear and reduced stress in the part.


As the flow front reaches the end of fill, the increasing cavity pressure helps equalize the flow balance differences between cavities. Some part features can also have the same effect on the balance and may not be at the end of fill. For example, the tamper band on a closure can “choke” or “meter” the flow through that area of the part. In this case, it would be best to perform troubleshooting procedures before those features take effect.
For Percentage-of-Fill, balance is evaluated at the transition point between velocity control and pressure control (V/P switchover). For a 48-cavity tool with a 5-gram part, a processor would evaluate balance at 90% or 95% of the total shot weight of 240 grams. The Percentage-of-Fill method serves as a tool to identify outliers (parts filled less than 90%) at the transition from velocity control to pressure control. Parts that are less than 90% full at the transition point could have molding defects.
The First-to-Fill method is more suited for troubleshooting, to investigate specific defects or problems with the molding system. Transition point (V/P switchover) is set so that the first part to fill is the desired percentage of the final part weight. All other parts will weigh less than this first part to fill. For example, the first part to fill is 95% of the final part weight.
Processors should manage their expectations when measuring the short shot balance of their injection molding process. The first step is to determine what procedure is right for the processor. Husky recommends the Percentage-of-Fill method (95%). The next step is to set a realistic expectation for the procedure, with the understanding that systems with valve gating typically deliver better balance than thermal gating systems. These are fair expectations that need to be tempered, since other factors can adversely influence variation and ultimately short shot balance.
If the mold under qualification exceeds these values, the process should continue. Investigate the results, and if the issue is not identified, document the results and continue with the qualification. If there is an issue (e.g., dimensional problem), a troubleshooting balance study should be completed to look for correlation.
In one example with a 144-cavity hot tip system, two contamination issues were resolved. Balance improved from 67% to 85%, and finally to 93%. In another example, the greatest influence on balance was the mold’s cooling water pressure.
It should be understood that short shot balance testing represents only a confirmation step, which attributes a variation measurement to the mold. It does not cast any negative judgement regarding the design, construction and function of the overall hot runner design.
Conclusion
Short shot balance plays an important role in optimizing the injection molding process. One of the most important goals of balance measurement is to minimize variation between the cavities by measuring part weight. Short shot balance measurement is an important evaluation tool that can be used during mold qualification to troubleshoot specific issues. There are different procedures that can be used to check short shot balance, with varying results on the same system. It is important to pick the best procedure to fit the needs of the process and match the expectations to the procedure.
Several factors influence the short shot balance performance of a specific tool. Addressing the imbalances of a molding system requires a focused look at influences on variation. A reduction in process variation involves improvements in all aspects of the processing system. The hot runners can have a significant influence on short shot balance, and this is one of the most common considerations during mold qualification. Husky optimizes factors to minimize variation and improve consistency, including 100% geometrically balanced hot runner system designs, thermally uniform hot runners with precise temperature control and the elimination of gate open-close variation with Husky UltraSync technology.